Introduction
Diesel generators play a crucial role in providing backup power during emergencies and ensuring continuity of operations in various settings such as hospitals, data centers, and industrial facilities. However, to ensure the safe and reliable operation of diesel generators, it is essential to implement robust safety monitoring systems. This article explores the importance of safety monitoring for diesel generators, the key components of a safety monitoring system, and best practices for enhancing safety in diesel generator operations.
Importance of Safety Monitoring for Diesel Generators
Safety monitoring for diesel generators is essential for several reasons. Firstly, diesel generators are typically used as backup power sources during emergencies or power outages, which means they need to function reliably when called upon. Regular monitoring helps detect potential issues early on and ensures that the generator is in optimal condition to provide power when needed.
Secondly, diesel generators operate using combustible fuel, making them a potential fire hazard if not properly maintained and monitored. Safety monitoring systems can help detect overheating, fuel leaks, or other malfunctions that could lead to a fire and take corrective actions to prevent accidents.
Furthermore, diesel generators emit exhaust gases that can be harmful to human health if not properly ventilated. Monitoring systems can track emissions levels and ensure that the generator is operating within safe limits to protect both the environment and individuals working in the vicinity.
Key Components of Safety Monitoring Systems for Diesel Generators
A comprehensive safety monitoring system for diesel generators typically includes the following key components:
1. Remote Monitoring and Control: Remote monitoring allows operators to track the performance of the diesel generator from a centralized location. This includes monitoring fuel levels, battery status, engine temperature, and other critical parameters in real-time. Remote control capabilities enable operators to start, stop, or adjust the generator settings as needed without physically accessing the equipment.
2. Alarms and Notifications: Safety monitoring systems are equipped with alarms and notifications that alert operators to potential issues or anomalies. These alarms can be configured to trigger based on predefined thresholds for parameters such as temperature, fuel levels, oil pressure, or battery voltage. Timely alerts help operators take corrective actions promptly to prevent equipment damage or downtime.
3. Automatic Shutdown Mechanisms: In the event of a critical fault or malfunction, safety monitoring systems can trigger automatic shutdown sequences to prevent further damage or hazards. These shutdown mechanisms are designed to protect the generator and surrounding equipment from catastrophic failures and ensure the safety of personnel working in the vicinity.
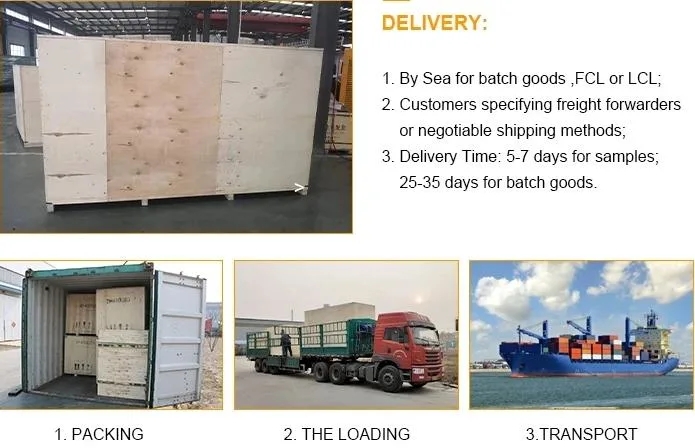
4. Data Logging and Analysis: Safety monitoring systems record and store historical data on the performance of the diesel generator, including operating hours, load profiles, maintenance schedules, and alarm history. This data can be analyzed to identify trends, predict potential failures, and optimize maintenance schedules for improved reliability and efficiency.
5. Environmental Monitoring: In addition to monitoring the performance of the diesel generator, safety monitoring systems may include environmental sensors to track parameters such as exhaust emissions, ambient temperature, and humidity levels. This data helps ensure compliance with environmental regulations and provides early warning of any environmental hazards associated with generator operation.
Best Practices for Enhancing Safety in Diesel Generator Operations
To enhance safety in diesel generator operations, operators can follow these best practices:
1. Regular Maintenance and Inspections: Implement a routine maintenance schedule for the diesel generator, including regular inspections of critical components such as filters, belts, hoses, and electrical connections. Perform oil and filter changes as recommended by the manufacturer to prevent engine wear and ensure optimal performance.
2. Training and Certification: Ensure that personnel responsible for operating and maintaining the diesel generator are properly trained and certified. Training should cover safe operating procedures, emergency shutdown protocols, and basic troubleshooting techniques to handle common issues effectively.
3. 300KW Diesel Generator For Sale Planning: Develop an emergency response plan that outlines procedures for responding to generator failures, fuel leaks, fires, or other emergencies. Conduct regular drills to test the effectiveness of the plan and ensure that all personnel are familiar with their roles and responsibilities in case of an emergency.
4. Fuel Quality Management: Monitor the quality of diesel fuel stored for the generator to prevent contamination, degradation, or microbial growth that can affect engine performance. Use fuel additives as recommended by the manufacturer to improve fuel stability and combustion efficiency.
5. Air Quality Monitoring: Install air quality sensors near the exhaust outlet of the diesel generator to monitor emissions levels and ensure compliance with regulatory limits. Implement proper ventilation systems to minimize exposure to harmful gases and particulate matter in the surrounding environment.
6. Battery Maintenance: Regularly inspect and test the batteries used to start the diesel generator to ensure they are in good condition. Monitor battery voltage levels and replace batteries as needed to prevent starting failures during an emergency.
7. Record Keeping and Documentation: Maintain detailed records of maintenance activities, inspections, alarm events, and operational data for the diesel generator. Keep a logbook with service reports, parts replacements, and any modifications made to the equipment for reference and compliance purposes.
Conclusion
Safety monitoring plays a critical role in ensuring the safe and reliable operation of diesel generators in various applications. By implementing a comprehensive safety monitoring system that includes remote monitoring, alarms, automatic shutdown mechanisms, data logging, and environmental monitoring, operators can enhance safety, prevent accidents, and optimize the performance of diesel generators. Following best practices such as regular maintenance, training, emergency response planning, fuel quality management, air quality monitoring, battery maintenance, and record keeping can further improve safety and mitigate risks associated with diesel generator operations. By prioritizing safety and implementing proactive measures, operators can maintain a secure and efficient backup power supply for critical systems and infrastructure.